Integrated Product Development
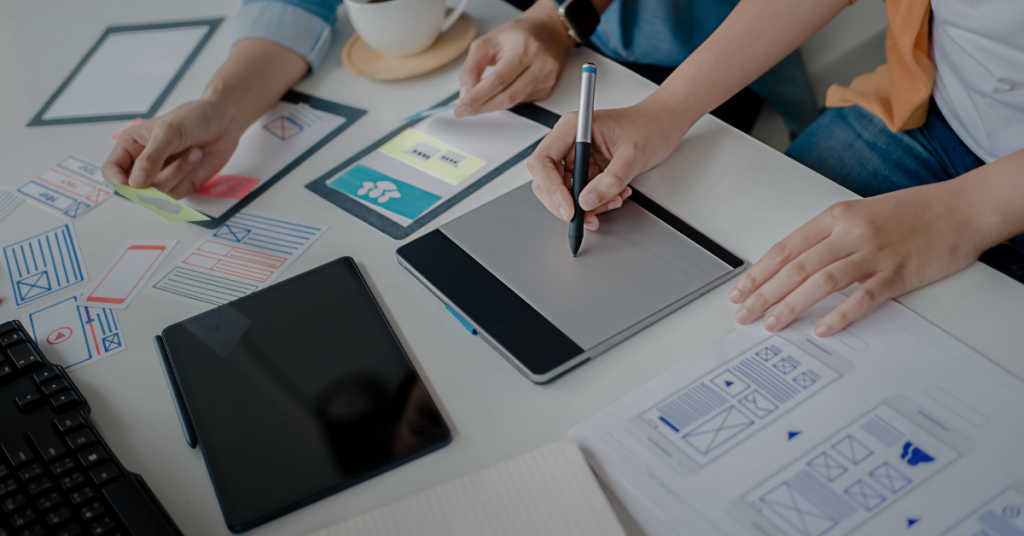
Have you ever wondered why the items we use every day look this way?
Cars, household appliances, and other products have long been a work of art, in the process of developing which involves a huge number of people from a variety of departments and fields of activity. But how do they manage to achieve a balance between the three fundamental components-product quality, time, and cost?
What is Integrated Product Development?
Integrated Product Development (IPD) is a framework that helps management and active project teams achieve innovative goals. IPD is a management system that promotes the simultaneous integration of multidisciplinary teams and parallel engineering. By leveraging the development lifecycle concept and involving all team members early in the design process, products become more customer-centric and achieve performance goals with fewer edits and costs.
This type of development has its own traditional approach, it became known as “throw it over the wall”.
The traditional approach came with the industrial revolution, assembly lines, and task specialization. In this approach, each team member passes the task to the next team member after completing the task. The approach aims to consistently complete tasks with minimal communication between team members, which in theory should reduce product development time.
The main advantage of this approach is only that in complex projects it is easier to track the degree of readiness of the project. But, in reality, everything always goes wrong. There is a need to make changes, which forces you to throw the task back a couple of walls, fix it and re-start the flow. The lack of a built-in communication system only increases the project time.
The approach has two fundamental paradigms:
- product teams (sometimes also called cross-platform teams),
- parallelization of tasks and work.
There are no walls over which to throw information. All team members are involved in the development from the earliest stages and each team member is responsible for the implementation of the project, not just their part.
At first glance, it may seem that this approach will only increase the development time since we involve employees at a stage when they can not yet start working due to the lack of input information for them. But, this is just a myth.
Practice shows that IPD allows you to reduce the development time by an average of 60%, and the number of changes by an average of 15 times.
Integrated Product Development in Hardware and Software
The main goal of IPD is to minimize design changes at later stages, reduce project risks, and reduce costs. This is true for both hardware and software development.
Everyone knows that integration is quite a complex process, especially for the development of high-tech products. And oddly enough, the best approach to address this complexity is to integrate hardware and software components as often as possible, in small increments, and even in real-time as new integrations become possible.
This is explained by the fact that such small steps are most easily managed if the different people involved work in the same team. Combining electrical engineers, mechanical engineers, and firmware engineers into a single Scrum team is considered the ideal way to weed out integration errors as soon as possible.
Main Pros and Cons of Integrated Product Development in Hardware
The most important feature of IPD is that the products are planned in the context of the overall corporate strategy, which determines why and when the product development will begin, what systems it will incorporate, and what technologies will be used. These processes go hand in hand with the “voice of the consumer”, which determines the key requirements for the system.
PROS:
- Smoother product development at all stages
Thanks to flexible development and an integrated approach, the product will be created faster. It will also be able to start marketing promotion earlier, which will speed up the receipt of early investments.
- Integrated process design
Product production and support processes must be integrated with product design to optimize product performance, availability, and lifecycle cost. Understand the existing and planned capabilities and limitations of the process.
- Better cost management
IPD raises awareness of availability and lifecycle cost. Engage your development team members in plans and suggestions for new products or programs to get their input and commitment. This allows you to set target costs and follow these goals.
- Develop more robust designs
Quality and reliability assurance techniques, such as experiment planning, FMECA, etc., provide an effective way to understand the role and interaction of product and process parameters with performance or quality characteristics, resulting in robust designs and increased reliability. Apply “lessons learned” to avoid repeating past mistakes, and conduct formal design reviews to ensure that all design issues and risks have been properly addressed.
CONS:
- You need to configure/create processes
Since we said above that IPD is the easiest way to integrate into your hardware development using the Scrum methodology, you will need a specialist who will correctly configure all the processes and create dedicated teams for this.
- More time for planning
This is due to the fact that the hardware is difficult to upgrade in the future. In order to take into account all the needs in the future and lay additional resources for further development of the product, it is necessary to carefully design all possible options for further actions.
- Unusual flow of work for engineers
Since Integrated Product Development requires a greater commitment of specialists in the team, many will be uncomfortable at first to organize their daily routine and incomprehensible activities. This disadvantage can be covered by an intelligent specialist who will help at each stage of integration.
Takeaways
Using the IPD approach increases customer loyalty, reduces the cost of product development and production and reduces the time to market. Together, these advantages allow the company to be competitive not only in the domestic market but also to enter international markets.
The ability to complete more development cycles than the competition allows you to offer more options and product options, as well as gain additional experience in development and production. Companies that continue to use the traditional approach are experiencing a lack of technology in their products, which leads to a weakening position in the market in relation to competitors.
Recent Posts
- R&D as a Service: What It Means and When You Need It
- Prototyping Done Right: How to Avoid Costly Mistakes
- Why Emotional Intelligence is Key for Leadership in the Digital Age
- How AI is Being Used to Combat Climate Change
- Building an Inclusive and Diverse Tech Workplace: Why It Matters
- The Rise of No-Code and Low-Code Development: Is It the Future?